Car rack systems have become completely ubiquitous as engineers continue to invent creative ways for us to transport our equipment. Anything from the common bike rack, cargo boxes, racks, and kayak racks to specialized gear like skis and snowboards, fishing rods, motorcycles, and heavy tools like ladders.
Because of this wide application range, manufacturers continuously experiment with different materials for specific applications, and you’ll be faced with navigating those waters when you buy your next rack. In this article, we’ll discuss the primary materials used for rack manufacturing and the coatings applied and help you trade off the specific benefits and shortcomings of each when making a choice.
Car Rack Manufacturing Materials
There are primarily three materials used in the manufacturing of car rack systems, and we will discuss the pros and cons of each below:
Steel

Steel can rightfully claim to be the original car rack system material. It is readily available, durable, and strong. Steel is still the material of choice for many rack manufacturers with specific design goals and parameters.
Pros:
- High tensile strength, providing durability and longevity.
- It can be painted, powder-coated, or galvanized for protection and aesthetics.
- It is typically less expensive than some alternative materials.
Cons:
- Steel is heavier compared to aluminum and certain other materials.
- It can corrode if the protective coating is damaged or wears off.
- It’s bulkier in appearance.
Load-Bearing Capacity:
Steel has a high load-bearing capacity when compared to aluminum and composite materials. Its high tensile strength makes it an ideal material for racks with heavy loads. Because of this, you will find it commonly used to produce hitch cargo carriers, multi-bike racks, utility racks like ladder racks, and larger equipment racks.
Most Suited For:
If you are looking for a racking solution for one of the things below, you should consider a steel rack:
- Multiple bikes.
- Heavy cargo carriers.
- Roof-top tents and large equipment.
Aluminum

Aluminum has become a popular material for car rack manufacturing, and rightfully so. It is naturally corrosion-resistant and lightweight. Yet it is strong enough for car rack requirements for most equipment types, including bikes, kayaks, skis, cargo, and utility racks like ladder racks.
Pros:
- Lightweight, making installation easier and adding less weight to the vehicle.
- Naturally resistant to corrosion.
- Offers a sleek and modern appearance.
Cons:
- Depending on design and construction, it may not be as strong as steel.
- It can be more expensive than steel options.
- Vulnerable to scratches and dents.
Load-Bearing Capacity:
Aluminum has a medium load-bearing capacity compared to steel but a higher capacity than composite materials. Its light weight makes it ideally suited for racks and car accessories that must be frequently removed and remounted. It is great for medium loads and strong enough for most bike rack requirements.
Most Suited For:
If you are looking for a racking solution for one of the things below, you should consider an aluminum rack:
- Single or double bike racks.
- Lightweight kayaks or canoe racks.
- General-purpose roof racks for carrying luggage or camping equipment.
Composite Materials

Composite materials, like carbon fiber or fiberglass, are starting to impact the bike rack manufacturing landscape. Their extremely light eight and disproportional strength qualities make them suitable for some very specific rack applications. Racks constructed from composite materials are often much more expensive than steel and aluminum. Still, they do offer an alternative with specific pros and cons that can be considered.
Pros:
- Extremely lightweight.
- Offers high tensile strength (especially carbon fiber).
- It can be molded into aerodynamic and stylish shapes.
Cons:
- Expensive compared to steel and aluminum.
- It can be brittle and crack under severe impact.
- Not as easily repairable as metals.
Load-Bearing Capacity:
Composite materials are typically good for lighter loads, although the tensile strength of carbon fiber allows it to bear more weight than expected for its weight. These materials are often not used as the primary load-bearing material but are used in constructing and manufacturing complementary parts. That said, composite materials are available today and can serve as the primary material for several car rack applications. These technologies continue to evolve and improve.
Most Suited For:
If you are looking for a racking solution that can be described by the bullets below, you should consider a carbon fiber or composite material rack:
- Specialty racks (e.g., those used for racing bikes).
- Aesthetic or aerodynamic components of a rack system.
- Limited or niche applications in premium rack systems.
Plastic and Rubber Components
While most car rack systems are manufactured from the three materials discussed above, many components, like knobs, protective ends, handles, cradles, clamps, and fasteners, are made from plastic and rubber. Both these materials are lightweight and corrosion-resistant and ideally suited to provide cushioning, preventing damage to the gear.
They must be regularly checked with the rest of the rack, though, as they are prone to degradation over time due to UV exposure and general wear and tear.
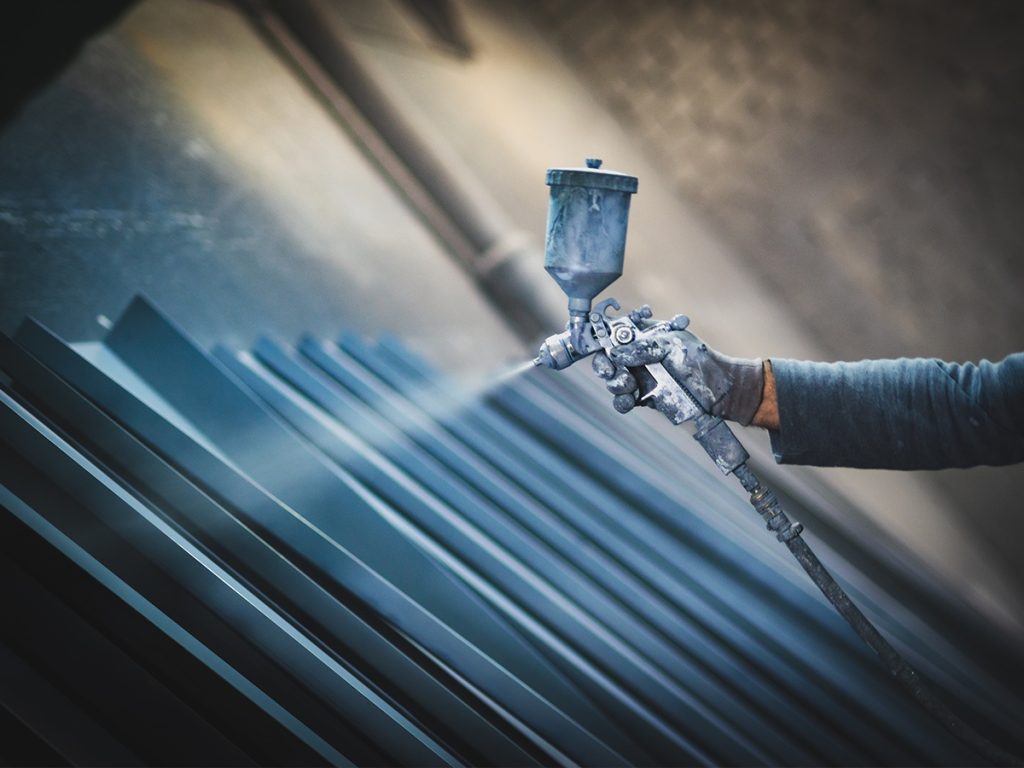
Coatings and finishes
Hand-in-hand with the material your car rack is manufactured from is the actual coating and finish applied to it. Coatings can have a substantial impact on the corrosion resistance of a rack, contributing to its longevity as well as enhancing its aesthetic appeal.
Not all finishes and coatings can be applied to all materials, though. Here’s an overview of the three most popular car rack coatings.
Paint
Various materials have long benefited from paint, serving as a strong age-old finishing tool for protection and aesthetics. It is simply a mix of pigments and a medium and can conveniently be applied through spraying, rolling, or brushing. It turns into a film that guards against the environmental impact while ensuring a range of finishes and colored results. Paint is widely employed for car racks and offers a custom touch and a refined look, but being prone to wear and chipping over time may require some touch-ups.
Powder Coating
With powder coating, metals undergo a defensive and sophisticated finalizing technique to obtain an elegant outcome. The procedure entails fine resin and pigment granules sprayed electrostatically onto the surface and then set with heat. The result is a consistent, long-lasting, and appealing finish. Its capability to endure impact, weather, and chemicals makes it the preferred choice for various objects that face constant exposure to the elements, including car racks.
Zinc Coating (Galvanization)
Zinc coating, frequently termed galvanization, is a frontline defense for metals, especially steel, against rust and corrosion. By applying a protective layer of zinc, the underlying metal gains enhanced resistance to environmental aggressors like moisture and salt. Due to this robust protection, galvanized finishes are prevalent in items prone to weather exposure, like car rack systems. The process extends the product’s life and minimizes maintenance by providing a self-healing mechanism for minor scratches.
The table below includes the pros and cons of each of these finishes and which of the primary materials it can be applied to.
Coating/Finish | Pros | Cons | Applicable to Materials |
---|---|---|---|
Paint | Color-matched; Additional corrosion protection; Aesthetic enhancement | Can chip/scratch; Requires maintenance | Steel, Aluminum, Composite |
Powder Coating | Durable; Resistant to chips/scratches; Seamless finish | Complex application; More expensive | Steel, Aluminum |
Zinc Coating | Excellent corrosion resistance; Long-lasting; Self-healing | Aesthetically less pleasing; Heavier; Rough texture | Steel (primarily, but can be used as a pre-coating for Aluminum) |
Conclusion
Several factors will inform your choice of material for your next car rack. Familiarize yourself with the pros, cons, and specific applications of this article’s materials and coatings and make an informed decision. This information should equip you with good questions to ask your dealer before purchasing.
Willem is an avid mountain biker and outdoor sports enthusiast. For years, he has been riding mountain bike stage races, including the grueling Cape Epic. As a father of three adventurous kids, he knows about packing a vehicle to haul his gear safely and responsibly from home to any exciting weekend or holiday destination.